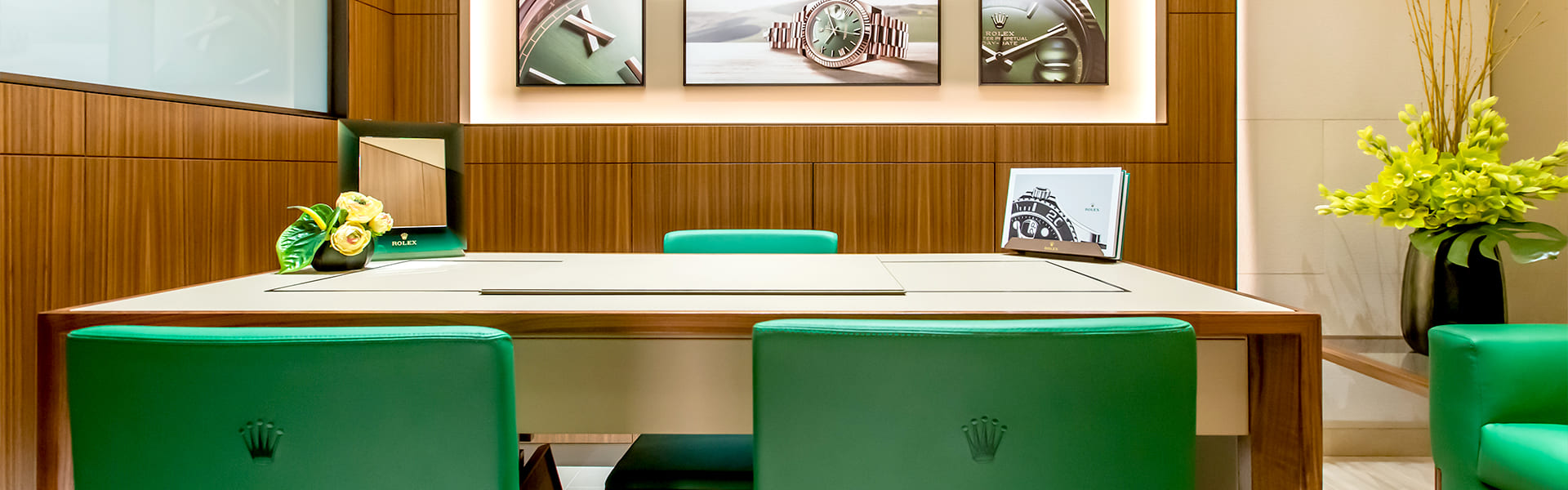
Luxury timepieces are designed to last a lifetime (or beyond), but from time to time they need some attention. Generally speaking, mechanical watches need to be serviced every four to ten years dependent on the brand.
If your Rolex, Tudor, or Patek Philippe needs service or repair, Kirk Jewelers offers factory service to make that process as convenient for you as possible.
We are proud to be a Rolex Authorized Service Center and among a handful of carefully selected Rolex-trained watchmakers recognized for their mastery and dexterously.
So what are the ten steps of a watch service:
STEP 1 – ESTIMATION
A cost estimate is offered by the factory as well as the estimated required amount of time to complete the work and return the watch to you. After you approve this step, the factory will commence with the work agreed upon.
STEP 2 – DISASSEMBLY
Removal of the bracelet or strap, and disassembly of the case and the movement. For the disassembly of both the case and the movement, special tools and extensive training are required.
STEP 3 – CLEANING
Once the case and the movement is disassembled, the individual parts are thoroughly cleaned in a deep ultrasonic/steam clean. The specially formulated solutions removes the old lubrication and any dirt from the movement.
A luxury watch can have hundreds of parts, each of them very fragile to handle, so the process is very delicate.
STEP 4 – REPLACEMENT PARTS
After the parts are cleaned, each one is meticulously examined for wear and tear. Worn or weak components are then replaced with genuine parts.
STEP 5 – ASSEMBLY
Each movement can contain hundreds of parts and the watchmaker painstakingly reassembles them. Precise lubrication is applied to the contact points in the movement to minimize friction and prevent wear. This helps ensure optimal performance and longevity of the timepiece.
STEP 6 – TIMING AND CALIBRATION
In several steps, the watchmaker adjusts the movement until the timepiece is operating at optimal precision. The calibration is key to meet the manufacturer’s timing tolerances.
STEP 7 – REFINISHING
The case and the bracelet of the timepiece is refinished to bring back its original luster if you desire. Otherwise, this step can be skipped if you prefer to leave the original condition to enjoy the worn in look.
As part of the polishing process, scratches and small dents are removed. Different compounds are used to provide the final finish – polished or matte – while preserving the original shape of each component.
STEP 8 – CASE ASSEMBLY
Lastly, the case is skillfully reassembled and all seals and gaskets are replaced to ensure the water resistance is back to factory standards.
STEP 9 – TESTING
Every watch pressure tested, to ensure water resistance or waterproofing.
STEP 10 – QUALITY CONTROL
Rigorous checks are carried out at each stage of the servicing process. During the final check, the power reserve, timing accuracy and aesthetic appearance of the watch is throughly checked. Then the customer is informed that the watch is ready for pick up.
IN CONCLUSION
As Official Jewelers for the brands we represent, we adhere to all factory requirements. For peace of mind, the factory service includes a 2 year warranty for every watch. Details about the work performed are listed on the invoice as part of the service history.